Committee Blog: Manufactured Product Safety — Vaporizer Delivery Devices
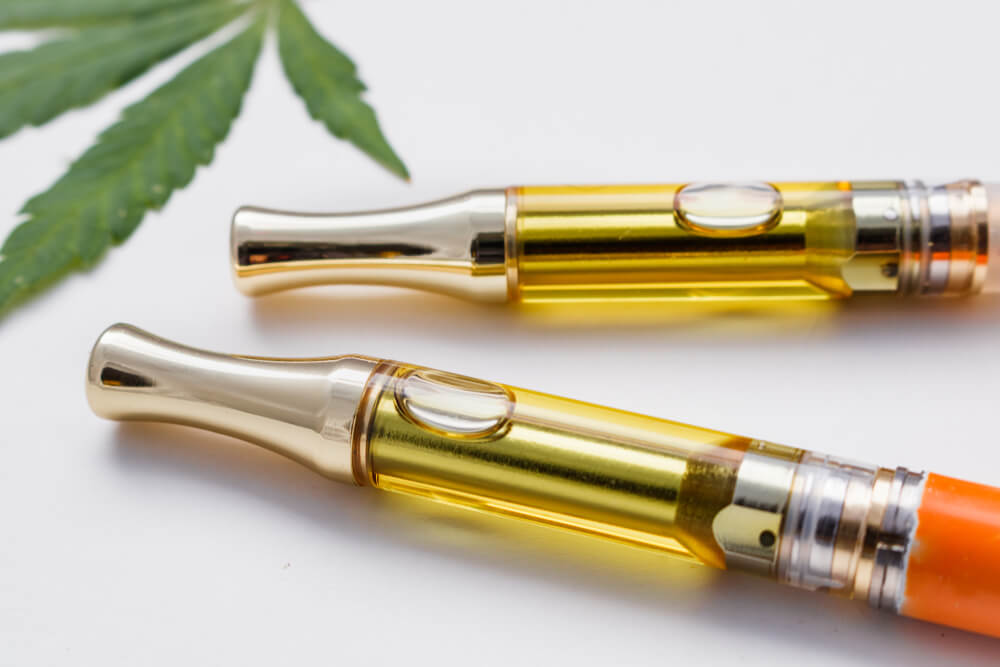
by NCIA’s Cannabis Manufacturing Committee
Product safety isn’t an endpoint, it’s a journey. That’s what we told you in the 2021 series premiere, and it continues to hold true. In the last post, we revisited the Vaporizer Liquid Formulations portion of the NCIA’s policy council white paper to provide guidance to the industry. This time, we’re republishing the Vaporizer Delivery Devices section below. We’ve learned more about EVALI since its original publication, and while some of the specifics may be a little dated, the principles remain relevant to helping you understand vapor product safety.
Over the course of the next several months, we’ll bring you new content with the following working titles.
The Importance of Testing Vapor Products as a System
Edibles Stability – Microbial Growth Due to Insufficient Packaging
Terpene Limits Across Multiple Product Formats
So, while we wait with bated breath for this exciting new content, enjoy the excerpt below!
Excerpted from The Key To Consumer Safety: Displacing The Illicit Cannabis Market Recommendations For Safe Vaping. Access the full report and citations.
Background
While the technology used to vaporize cannabis extracts have been around for many years, advancements in vaporization technology and supply chains over the past decade have led to widespread adoption and growth of vaporization as a preferred method of cannabis consumption. Vaporizer devices offer the benefits of being discreet, allowing for metered consumption, and eliminating carbon associated with combusting cannabis flower. However, not all vaporizer devices are created equal and manufacturers should develop an understanding of the nuances of different vaporizer devices to ensure the delivery of a safe and high-quality experience. Aside from considering experiential qualities such as taste and the amount of vapor produced, manufacturers should consider at least the following three categories of issues that can present safety risks.
Physical Design Considerations
Vaporizer devices should be mechanically and electrically safe. This starts with relatively basic considerations that include ensuring the device is mechanically sound, does not leak alkaline or heavy metals, and is not configured in a manner that presents a safety hazard. In the early 2010s, there were many reported instances of vaporizer devices exploding. This was primarily due to improper electrical design and battery cell protection. Battery cells that are not protected from drawing current beyond their rated capacity or are allowed to drain too deeply present a safety risk. In fact, this risk led to the development of the UL 8139 standard for e-cigarette battery safety and the FDA recently relaxed its prohibition on e-cigarette battery changes in order to allow manufacturers to comply with this standard. UL 8139 is applicable to vaporizer devices and anyone who sources or develops a vaporizer device for the cannabis market should voluntarily comply.
Contamination by Hardware
Vaporizer device hardware should be tested for the presence of heavy metals. Currently, some manufacturers use Restriction of Hazardous Substances (RoHS) testing or rely on vendor representations that the components and materials being used are certified as FDA food-grade. The California Bureau of Cannabis Control mandated heavy metals testing standards for the three categories of cannabis products, including inhalable cannabis products, starting on December 31, 2018.
Vaporizer device hardware that comes into contact with cannabis formulation should also be free of other contaminants. It is important to consider both contaminants that could be immediately detectable in vaporizer devices as well as those that can be released or created over time. Vaporizer devices are designed using a variety of industrial manufacturing processes, some of which can leave residual oils, biological agents, or other substances in the device. It is important that device manufacturers clean incoming components, assemble them in a clean environment, then store and ship them in a manner that prevents re-contamination. Depending on the nature of the component, one or more of a cleaning bath or ozone treatment may be used for cleaning. After cleaning, assembly of vaporizer components should be performed in a cleanroom environment under appropriate current Good Manufacturing Practices (cGMP). Unfortunately, simply asking a device manufacturer whether it operates in such a manner is not sufficient to be certain that it does. There is no substitute for first-hand inspection of manufacturing processes. While it may not be practical for U.S.-based cannabis manufacturers to maintain a constant presence in the country of manufacture, it is possible to hire local agents who are skilled in audit practices and can perform unannounced inspections to verify that desired practices are implemented within the supply chain.
As noted above, hardware may also introduce contamination into the formulation over time, either through the process of leaching heavy metals or through chemical reaction. Leaching is a process whereby soluble constituents that may be present in materials dissolve into a formulation. A well-known example was the discovery that plasticizers present in certain plastic food and beverage containers were leaching and then being consumed. As a result, new types of plastics were developed for improved food safety. Vaporizer components that contact cannabis formulations may present a similar issue and leaching may be tied to metals, ceramics, plastics, or other materials. In addition to leaching, certain materials may react with cannabis formulations, especially those with high terpene content which tends to be more volatile. Moreover, metal components in contact with formulations may be especially susceptible to leaching and lead to contaminants such as heavy metals in the formulation.
The good news is that it is possible to address this risk of leaching through the use of appropriate base materials and or plating. Base materials such as stainless steel are good candidates because of their low tendency to react with formulations. Plating other materials with corrosion-resistant metals is also possible; however, care must be taken to specify the right material and plating thickness while also ensuring the plating is not damaged during assembly.
With proper material selection and design, it is possible to reduce the risk of such contamination, including through conducting stability tests. In a stability test, a formulation is placed into the vaporizer device for a period of time, then removed and tested for contaminants. A good guide is to design the stability test to align with the desired shelf life of the product. That doesn’t necessarily mean the test needs to be as long as the rated shelf life. Typically, elevated temperature tests are used to determine stability and can cut the duration of the test to 50% or less of the desired shelf life. In addition, by taking measurements at intermediate intervals, stability can be better characterized and the point at which contaminants would exceed their respective limits can be projected.
Device Impact on Formulation: Control the Heat
The most fundamental, yet perhaps the most underappreciated aspect of vaporizer devices is how they vaporize cannabis formulations. Setting aside dry herb vaporizers, all liquid cannabis vaporizers basically work by bringing the formulation into contact with a hot surface in order to heat it and thus create vapor. While this may seem straightforward, there are a number of subtleties that affect the outcome. First, the temperature of the hot surface must be hot enough to heat the liquid, yet not so hot as to cause components of the formulation to degrade into byproducts that could be harmful. In fact, one study demonstrated how changing the voltage, and thus the temperature of an unregulated vaporizer device can affect the production of such degradants. While more advanced vaporizer devices attempt to control vaporization temperature by using heating elements made of specific materials that indirectly measure temperature and regulate the power delivered to the heating element, the majority do not.
Different formulations have different compositions and contain constituents that vaporize and degrade at various temperatures. This means that to fully control vaporization, the vaporizer device must be configured precisely to the requirements of the formulation in use. Second, many vaporizer devices do not heat uniformly. Rather, the heated surfaces heat unevenly, creating hot spots that can locally trigger thermal degradation. Temperature control circuits typically measure an average temperature and do not prevent such hot spots. Finally, the majority of vaporizer devices, whether they contain fiber wicks or ceramic, rely on capillary action to bring the formulation into contact with the heated area or surface. During a puff, capillary action is also what replenishes the formulation at the heated surface, and such capillary replenishment takes time. Depending on the viscosity of the formulation and the duration of the puff, a heated surface that was initially saturated with the formulation can become dry and hot during the course of a puff. Experienced users sometimes refer to this as a “dry hit,” which can be perceived when a cartridge runs dry or during a long puff. Dry hits can result in increased thermal degradation.
Armed with this understanding of the nuances of vaporizer devices, one can appreciate how the common business model of selling cartridges with a universal 510 threaded connection that can be used in conjunction with any number of batteries, any number of power settings, and filled with a variety of formulations makes it difficult to guarantee what is produced during vaporization. In order to understand and control the output of a vaporizer device, the system should be designed, configured, and tested as a whole; cartridge and battery, plus formulation. Closed systems with proprietary connectors and one-piece designs do not face the cartridge-battery mismatch challenge, but should still be tested in conjunction with the target formulation using a reasonable worst-case puff duration. And while new systems under development that employ non-contact heating methods may not present the same temperature control challenges, they too should be validated as a whole.
The Cannabis Manufacturing Committee (CMC) focuses on reviewing existing business practices and state regulations of concentrates, topicals, vaporizers, and edibles, ensuring the manufacturing sector is helping shape its destiny.