Committee Blog: A Guide to Navigating Cultivation Environmental Requirements
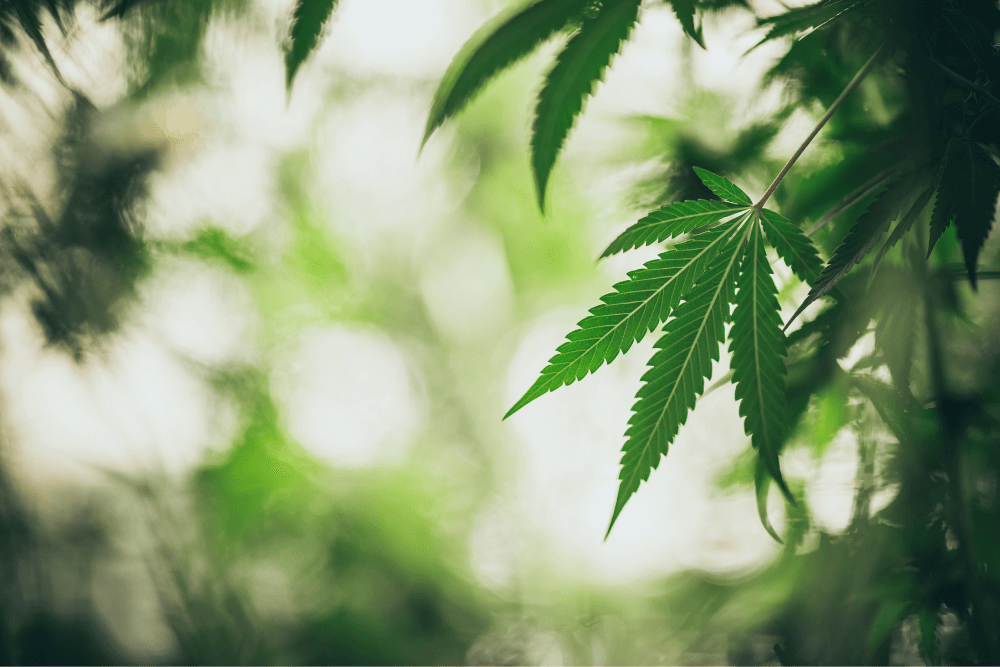
Navigating environmental requirements and reviews can be one of the most challenging and costly aspects of obtaining a cannabis cultivation license. Environmental standards and regulatory requirements differ from state to state and within local jurisdictions. While regulations may vary, cannabis operators encounter similar environmental requirements nationwide. Environmental reviews and impact assessments require an evaluation of cultivation policies and operations for sediment and erosion control, water usage, wastewater discharge, energy efficiency and carbon footprint, air quality, and odor control. This guide will aid operators in establishing the best practices for these environmental concerns to create a smoother environmental review process for the cultivator.
Sediment and Erosion Control
Sediment and erosion control methods are required for outdoor cultivation to ensure the facility has a comprehensive mitigation plan to prevent adverse effects the outdoor crop may cause to the land. Sediment controls are structural measures intended to complement and enhance the implemented erosion control practices and reduce any sediment discharge. Erosion control is a soil stabilization process consisting of mitigating measures to prevent soil particles from detaching and moving into stormwater runoff. Ensuring this compliance may include implementing Best Management Practices (BMPs) for Sediment and erosion control. These BMPs should be implemented before the onset of the rainy season, typically in October. Sediment and erosion control devices and measures should be replaced when they deteriorate.
Sediment Control BMPs
- Silt fences
- Fiber rolls
- Hydroseeding
- Sediment Trap
- Inspect the trap on a routine schedule for litter and debris
- Remove the sediment built up in the trap and sprinkle it lightly over vegetated areas to increase soil fertility
- Gravel bag berms
- Sandbag barriers
- Straw bale barriers
- Observation station on the property for visual monitoring of sediment pollution
- Add gravel to dirt roads
- Add stormwater detention basins
Erosion Control BMPs
- Vegetative Swales & Buffers
- Swales should be trimmed to prevent restriction of flow
- Routinely monitor for any debris and overflow
- Buffers should be added to the edges of parking lots and storage areas
- Placement of straw mulch over disturbed land
- Should be replaced often
- Soil binders
- Vegetation preservation
- Vegetation replacement for any disturbed areas that will not be in use
- Seed mixes containing native grass and wildflowers
- Hydroseeding
- Earth dikes
Waste Usage and Wastewater Discharge
Water usage and wastewater discharge management plans are required to ensure the cultivation facility legally and efficiently obtains its water and that no hazardous water is dumped onto the land surface, directly into the ground, or into another body of water where it could negatively impact the environment. Water usage may require obtaining documentation demonstrating you own the water rights to your facility or property. Cultivations connected to their municipalities’ water district may only need to report that information to meet this requirement. Such a facility may also need to contact its water provider to create a water rights letter showing the operator has the right to use that water. Cultivations that use other water supply methods, like wells, may need to provide a detailed report of their water quality and have well flow testing performed. Depending upon your state, you may also need to show how your water will be conserved. A cultivator may be required to create a water conservation plan detailing the procedures implemented at the cultivation site to conserve water. Wastewater discharging typically will require a cultivation site to apply for a Wastewater Discharge permit. Wastewater discharging plans that thoroughly explain how the cultivation will discharge any hazardous wastewater and what mitigating practices will be implemented to prevent wastewater from entering the environment untreated are also frequent requirements for this process.
Water Conservation Methods
- Recycling irrigation systems
- Automated irrigation systems
- Precision emitters
- Watering more frequently throughout the day in smaller amounts
- Planting pots
- Divert the dehumidifying and cooling system’s piping into a holding tank to reuse the water for irrigation
- Use organic mulch around each plant to prevent moisture loss
- Rainwater harvesting, if allowed in your area
- Substrate sensors to monitor water saturation
Wastewater Discharge Measures
- Using planting pots to prevent excess runoff
- Vegetative swales and buffers to capture wastewater
- Recycling irrigation systems with reverse osmosis and ultrafiltration or thermal evaporation
- Recycling systems that don’t have a filtration system can hold any hazardous wastewater in a holding tank and have it transported to an approved wastewater treatment facility
- Substrate sensors for the prevention of excess runoff
- Stormwater runoff prevention
- Store pesticides, chemicals, and fertilizers indoors and away from any outdoor growing areas and in approved containers
- Covering wastebins
- Divert stormwater away from any stockpiled materials
Energy Efficiency and Carbon Footprint
Cultivation energy efficiency and carbon footprint reporting are becoming more popular among regulators as the country moves toward environmentally friendly practices. Energy efficiency may require the cultivation site to comply with specific requirements for equipment and lighting. Many licensing bodies also require an energy efficiency plan that details what mitigating measures the operator will implement to reduce energy costs. Carbon footprint reporting may require greenhouse gas emission (GHG) reporting, which can require a cultivator to purchase carbon offsets. Green energy plans are sometimes required; these plans demonstrate how the cultivation will utilize green energy options to reduce their carbon footprint.
Energy Efficiency
- LED lighting
- Automated irrigation systems
- Automated blackout curtains for greenhouses
- On-site composting
- Low-flow fixtures
- Split ductless air condition
- Chilled water systems for dehumidification
- Modulating hot gas reheat forced air systems
- Sensor motion lighting in rooms that aren’t frequently entered
- Adjust lighting schedules based on the weather if using mixed-light
- Installing solar panels
- Request an energy efficiency review from your utility provider
Carbon Footprint
- Sign up with a clean energy provider that partners with your utility company and reinvests the funds from the program into clean energy initiatives in your state
- Avoid generation use wherever possible
- Install renewable energy sources at your facility, like solar panels
- Replace pesticides with biocontrols using predatory insects
- Use recycled or biodegradable packaging, even for wholesale flower
- Cultivate companion plants that deter pests and attract beneficial insects
- Reduce or eliminate lighting requirements by establishing a greenhouse or outdoor cultivation facility
Air Quality and Odor Control
Air quality reviews may be triggered for cultivation facilities, including the requirement to obtain an air permit. Air permits allow an operator to release a limited amount of pollution within certain restrictions. Air quality reviews for cultivations are triggered by several factors based on the state requirements, some of which may include drying, processing, generator use, fugitive emissions, and pesticide application. If a cultivator is required to obtain an air permit, they will be licensed to perform those activities. Cultivations going through air quality reviews may need to provide an Air Quality Control Plan outlining the mitigation efforts the cultivator will make for air quality pollution. Odor Control Plans are one of the most common regulatory requirements for cannabis businesses. If your environmental review includes odor control and you operate an outdoor cultivation site, you may be required to conduct an odor control study on your facility. These studies use wind patterns to measure the distance the odor from your cultivation will travel. Based on your state or local jurisdiction’s requirements, an odor control study may require you to move the border of your canopy. Conversely, an odor control study may prove that your cultivation will not be a nuisance due to odor pollution, and no mitigating measures will be required. Odor control plans should detail precisely what mitigating measures the cultivator will implement and, if available, data on how effective those measures will be.
Air Quality Control Plans
- Wetting the surface of dirt roads during the dry season
- Encourage ride-share amongst your employees
- Reduce VOCs wherever possible
- This can include timing harvesting to reduce ozone impact
- Include a chemical usage plan that describes how pesticides, fertilizers, and other agents will be stored and disposed of in alliance with the manufacturer’s recommendations
- Detail how you will maintain Safety Data Sheets (SDS) on all chemicals at the facility
Odor Control Plans
- Indoor cultivations and greenhouses can implement the following measures:
- Use carbon filters
- Explain in your plan how carbon filters work, provide data on their filtration rates, which you can locate in the manufacturer’s guide, and how often you will replace them
- Use wet scrubbers for indoor cultivation or greenhouses
- Explain how the air is treated when it passes through the scrubber
- Implement biofiltration measures
- Explain how the air will pass through soil, mulch, or other organic matter to filter the air
- Use oxidization treatments through your facility’s ventilation system
- Explain how the process of oxidization removes odor
- Have open communication with your neighbors regarding odor
- Explain how you will speak with your surrounding neighbors about any odor concerns and request your neighbors contact you if they do smell odor so you can begin an assessment into structural or equipment failures and, if needed, implement further mitigating measures to your plan
- Use carbon filters
- Outdoor cultivations can implement the following methods:
- Hire a professional to do an odor study to prove your facility’s compliance
- Plant fragrant flowers around the exterior of the site
- Use oxidization treatments through high-pressure misting devices around your cultivation area
- Explain how the process of oxidization removes odor
- All cultivation types should have open communication with surrounding neighbors regarding odor
- Explain how you will speak with your surrounding neighbors about any odor concerns and request your neighbors contact you if they do smell odor so you can begin an assessment into structural or equipment failures and, if needed, implement further mitigating measures to your plan
As regulatory requirements vary across the country, cultivators should carefully read their regulations and contact state and local departments for guidance on requirements specific to their operations. A thorough understanding of what plans must be created, studies performed, and special permits obtained will create a smooth environmental review process. Join the upcoming NCIA webinar from the Cannabis Cultivation Committee to dive deep with industry professionals on navigating environmental reviews across the United States.