Member Blog: The Importance of Storing Cannabis Properly
Cannabis is affected by humidity.
Yes, cannabis is definitely affected by humidity. Cannabis plants are sensitive to changes in temperature and humidity levels, both during cultivation and after harvesting.
During cultivation, cannabis plants need a specific range of temperature and humidity levels to thrive. Too much humidity can lead to the growth of mold and mildew, while too little humidity can cause the plants to dry out and become brittle.
After harvesting, cannabis buds need to be dried and cured to preserve their quality and potency. During this process, it is important to control the humidity levels to ensure that the buds dry slowly and evenly. If the humidity levels are too high, the buds can become moldy, while if they are too low, the buds can dry out too quickly and lose their potency.
In addition, the humidity level can also affect the storage of cannabis. If the humidity levels are too high, it can cause the buds to become moldy, while if they are too low, it can cause the buds to become brittle and lose their flavor and potency.
Therefore, it is important to control the humidity levels during the cultivation, drying, curing, and storage of cannabis to ensure that the buds are of high quality, potent, and safe for consumption.
How can dry cannabis lose potency?
When cannabis is dried and cured, it naturally loses moisture. However, if the cannabis becomes too dry, it can begin to lose potency.
This is because the active compounds in cannabis, such as THC and CBD, are stored in the trichomes on the surface of the buds. When the buds become too dry, the trichomes can become brittle and break off, causing the loss of these valuable compounds.
In addition, when cannabis becomes too dry, it can also affect the flavor and aroma of the buds. The terpenes, which are responsible for the characteristic smells and tastes of different strains, can degrade over time if the buds are too dry.
Therefore, it is important to store cannabis at the correct humidity levels to ensure that it stays fresh and potent. The ideal humidity range for storing cannabis is between 59% and 63% relative humidity. If the buds become too dry, you can try to rehydrate them by adding a humidifying device, such as a moisture pack, to the storage container. However, it is important to be careful not to add too much moisture, as this can cause the buds to become moldy or develop other quality issues.
Cannabis potency versus humidity
The potency of cannabis can be affected by humidity levels. When cannabis is stored at a high humidity level, it can cause the breakdown of THC and other cannabinoids, decreasing potency. On the other hand, if cannabis is stored at a low humidity level, it can cause the buds to become dry and brittle, which can also lead to a decrease in potency.
Therefore, it is important to store cannabis in a controlled environment with the appropriate humidity level. This can be achieved using specialized storage containers, such as airtight jars or humidors, designed to maintain a consistent humidity level. It is also important to monitor the humidity levels regularly and adjust as necessary to ensure that the cannabis stays fresh and potent.
Cannabis taste versus low humidity
When the terpenes are lost, the flavor of the cannabis can become harsh, bitter, or stale. This can make the smoking experience less enjoyable and may also indicate a decrease in potency.
If the buds have become too dry, it is possible to rehydrate them by adding a humidifying device, such as a moisture pack, to the storage container. However, it is important to be careful not to add too much moisture, as this can cause the buds to become moldy or develop other quality issues.
Member Blog: From Seed to Harvest – A Guide to Successful Cannabis Cultivation
by Erika Cruz, Outreach Monks
As the cannabis market continues to experience exponential growth, cannabis business professionals are constantly seeking ways to capitalize on this booming industry.
With the market projected to expand from USD 28.266 billion in 2021 to an astounding USD 197.74 billion in 2028 at (a CAGR) of 32.04%, it’s evident that there is immense potential for success in the cannabis sector.
However, to truly thrive in this competitive landscape, it’s crucial to have a solid understanding of the cultivation process from seed to harvest. That’s why in this guide, we will walk you through the essential steps and best practices for successful cannabis cultivation.
Let’s begin!
Choosing the Right Seeds
The first step in successful cannabis cultivation is selecting the right seeds. With a variety of strains available at a seed shop, it’s important to consider your preferences and goals. Are you looking for high THC content or a strain that offers more CBD? Do you prefer a Sativa or an Indica-dominant plant?
Invest time researching and selecting the best seeds to lay a strong foundation for your cannabis cultivation journey. You can even contact the seed shop and discuss your goal and get their recommendations.
Germination
Once you have your seeds, the next step is germination. It is the initial stage of cannabis cultivation, where the seeds begin to sprout and develop into seedlings. Here, the seeds absorb water, triggering biochemical changes that activate growth.
Start by soaking the seeds in a glass of water for about 24 hours to encourage the process. Then, transfer the seeds to a moist paper towel and place them in a warm and dark environment. Within a few days, the seeds will crack open, and tiny root and shoot structures will emerge, signifying the successful initiation of the growth cycle.
Seedling Stage
The next step is to transfer them to a growing medium. Use small pots or seedling trays filled with light, airy soil mix. Make sure the soil is moist but not overly saturated. Provide your seedlings with 18-24 hours of light daily, preferably using fluorescent or LED grow lights.
Maintain a temperature of around 70-75°F (21-24°C) and ensure proper ventilation to prevent mold or fungal growth.
Vegetative Stage
During the vegetative stage, your cannabis plants will focus on growing leaves and branches. To promote healthy growth, give your plants at least 16 hours of light daily. You can use specialized grow lights or take advantage of natural sunlight if growing outdoors. Also, maintain a temperature range of 70-80°F (21-27°C) and monitor humidity levels to avoid excessive moisture.
Using nutrient-rich fertilizers with higher nitrogen content is also recommended during this stage. It supports robust vegetative growth and prepares the plants for the subsequent flowering phase. Follow the instructions on the fertilizer package for dosage and frequency.
Note: Ensure the soil is evenly moist but not waterlogged when watering. Overwatering can lead to root rot, so allow the soil to dry out slightly between waterings.
Flowering Stage
After a few weeks of vegetative growth, your cannabis plants will enter the flowering stage. To initiate flowering, you must adjust the light cycle to 12 hours of light followed by 12 hours of complete darkness. (This is also known as photoperiod lighting.)
This change in light schedule signals the plants to begin producing flowers. However, it’s crucial to maintain consistent light and dark periods to avoid stressing the plants. Also, remember that the length of the flowering stage varies depending on the strain, typically lasting 8-10 weeks.
Harvesting
The moment you’ve been waiting for has arrived—it’s time to harvest your cannabis. Look for signs that the plants are ready, such as the appearance of trichomes (tiny, crystal-like structures) on the flowers. Trichomes will change from clear to cloudy or amber, indicating the optimal time for harvesting.
Use a magnifying glass or a microscope to examine the trichomes closely. Once ready, carefully cut the branches and trim away the excess leaves. Keep in mind that harvesting too early or too late can impact the potency and overall quality of your final product. So, be patient and wait for the optimal time when the trichomes have reached their desired color and maturity.
The Bottom Line
Successful cannabis cultivation is a multifaceted process requiring attention to detail, patience, and continuous learning. By following the guidelines outlined in this guide, you can ensure a high-quality yield, positioning yourself as a leading player in the rapidly expanding cannabis industry.
Author Bio: Erika Cruz is a content writer at Outreach Monks, a leading marketing agency known for its innovative digital solutions. With her expertise in crafting compelling copy and engaging content, Erika helps clients build their brands and connect with their target audience.
Committee Blog: Hop Latent Viroid (HLV) – Overview of Pathogen Biology, Spread, Control, and Testing
by Sarah Taylor-Laine (NCIA Education Committee, NCIA Cultivation Committee)
Hop Latent Viroid (HLV/HpLV), sometimes referred to as “dudding” or “stunting”, is one of the most pressing biological threats facing the cannabis industry worldwide. In the United States, HLV was first detected in California in 2017. Subsequent research by Dark Heart Nursery indicated that 90% of Californian facilities tested at the time were positive for the pathogen. The Dark Heart Nursery research team estimated that an HLV epidemic could result in up to US$4 billion in losses to the cannabis industry annually. To add insult to injury, HLV-infected cannabis may be linked to cannabis hyperemesis syndrome (CHS), which affects both adults and children.
As the name suggests, HLV was first detected in hops (Humulus lupulus; Cannabaceae). Outside of the United States, HLV has been detected in hops in New Zealand, the United Kingdom, South Korea, Japan, Brazil, the Czech Republic, Poland, Slovenia, Germany, China, Belgium, Turkey, and Canada. Within the United States, HLV has been detected in hops in Washington, and in cannabis in California, Colorado, Nevada, Oregon, and Washington. However, these are only officially-published reports and given the worldwide occurrence, HLV is likely to be endemic to many locations not listed here.
Viroids are subviral pathogenic RNA molecules which replicate within host plants and are only approximately 1/50th the size of the smallest viruses. Specifically, HLV is a circular RNA molecule of approximately 256 nucleotides in length, which can assume a rod-shaped secondary structure. In hops, HLV has been shown to interact with other viruses and alter the gene expression patterns of host plants. HLV has been found to not only infect hops and cannabis, but also Dianthus deltoides, Chenopodiastrum murale, Dysphania pseudomultiflora, cowpea (Vigna unguiculata), common bean (Phaseolus vulgaris), and stinging nettle (Urtica dioica). Notably, by subjecting hop plants to heat stress, researchers have been able to induce “thermomutant” HLV variants which could then infect both tomato (Solanum lycopersicum) and Nicotiana benthamiana, opening up the possibility that HLV could spread to new plant species under climate change-induced warming scenarios.
HLV often does not produce obvious symptoms in hops, and where they do occur there may be a long latency period, making control difficult. In hops, HLV is often detected early in the season at the plant base, where it gradually spreads up the plant and can be detected in all aerial tissues by mid-season during the flowering period. In cannabis, HLV causes brittle stems, a horizontal growth habit, and the destruction of flowers and trichomes. In both hops and cannabis, HLV may cause pathology in host plants through RNA interference (RNAi). HLV infection is reported to reduce THC content by 50-70%, which is not surprising as glandular trichomes are the source of THC in cannabis. In hops, HLV infection has been shown to reduce the content of terpenes and other secondary metabolites in susceptible varieties. It is currently unknown whether HLV infection decreases the terpene content in cannabis, but it is very likely.
In hops, HLV is not readily transferred by seeds, but may be transferred in uninucleate pollen. However, activating pollen nuclease HBN1 was shown to eliminate HLV in mature pollen. “Real world” transmission of HLV appears to primarily occur through the use of contaminated cutting tools, the use of infected plant materials, or from plant-to-plant. However, as an obligate pathogen, HLV requires living host tissue in order to survive and propagate. HLV has been confirmed to be transmitted between hop plants by potato aphid (Macrosiphum euphorbiae), green peach aphid (Myzus persicae), and hop aphid (Phorodon humuli), and may also be transferred by other herbivorous insects. Planting cannabis on sites previously planted with infected host plants is likely to be a source of infection, although this has not been experimentally verified.
In hops, chilling plants at 2-4 °C (approximately 35-40 °F) for 8-21 months prior to harvesting meristem tips for propagation has been shown to reduce or eliminate the spread of HLV, although the effect may be variety-specific. In addition, subjecting hop mericlones to heat treatment cycles (25-35 °C/77-95 °F for two weeks) has been shown to reduce HLV incidence by 70-90%. In terms of waste management, anaerobic fermentation at 70 °C (158 °F) causes HLV degradation, although standard ensiling does not appear to be effective. As with most viral and viroid diseases, there is currently no cure available to disinfect mature host plants. However, researchers are currently studying whether RNAi may have utility in cannabis crop protection against viral and viroid infections. Therefore, it is currently recommended to test all stock plants to confirm that they are pathogen free and to destroy all infected materials.
Plant materials can be tested for HLV infection using several molecular techniques, including DNA barcoding, RNA sequencing (RNA-seq), recombinase polymerase amplification (RPA), quantitative real-time polymerase chain reaction (qRT-PCR), reverse transcription PCR (RT-PCR), dot-blot hybridization, tissue print hybridization, in situ hybridization, and enzyme-linked immunosorbent assay (ELISA).
It is unknown how many, and which, lessons learned in hops will be transferable to cannabis. Both susceptibility and control of HLV in cannabis is likely to be variety-specific. To enable the breeding of HLV-resistant cannabis varieties, future research should focus on characterizing the molecular mechanism underlying HLV pathogenicity and host susceptibility. However, the situation remains that HLV is likely endemic in many cannabis growing regions and cultivators should focus on targeted biosanitation efforts to thwart HLV infection in their crops. These efforts should include testing all propagation materials for infection, destroying infected materials, sanitizing cutting tools and work surfaces, and limiting herbivory by sap-sucking insects such as aphids.
Sarah Taylor-Laine is a plant science polymath. Sarah has taught and developed college-level courses related to general biology, plant biology, and cannabis sciences at several institutions, most recently at Beal University. She has also worked across many industries including agriculture, horticulture, and arboriculture, performing diverse work in research, quality control, product development, regulatory affairs, scientific communication, and field-based consulting.
Member Blog: Cannabis Extraction – Creating a Competitive Advantage Through Data
By Jack Naito, president and co-founder, Luna Technologies
As customers become more sophisticated and discerning about the fast-growing cannabis extract market, from vapes to dabs to infused pre-rolls, the need to routinely produce consistent, quality extracts at scale is becoming doubly important for processors. Compounding the issue, the potential for federal legalization will bring significant growth opportunities but also increased federal oversight, including the need for Good Manufacturing Practices (GMP) and other onerous standards that will challenge unprepared operators.
Future-Proof Extraction Operations Through Data
To overcome these twin challenges, processors should start developing (if they have not already) a framework to capture, review, and analyze data at every stage of production to produce consistent, quality, and compliant products.
That framework should examine every aspect of the extraction process, starting with the type of material harvested from farms, including how it is stored and handled, through to the final, packaged retail-ready product.
It should also be tied to specific goals and clear objectives. Capturing data simply to capture data within a given framework but without a clear idea of how that data will be used can lead to analysis paralysis, or worse, endless trial-and-error that wastes time and material, eating into expected profits.
Leverage Design of Experiments Methodology
Design of Experiments, or DoE, is a scientific methodology that can help guide processors in determining the key parameters they want to track and how those parameters interact. This starts with assertions that map to specific goals or objectives, such as investigating the yield of a specific terpene with the goal of blending it with a distillate-based vape cartridge. From here, processors can design and set up experiments with varying inputs from temperature to pressure, to biomass composition, all to understand how the yield of a specific terpene is influenced throughout a given process.
When these learnings are applied at production scale, the framework developed through DoE methodology provides a guide for creating consistent products, but also to better manage and rectify issues that may arise. With specific goals in mind, processors can then determine what data they need to capture and analyze.
The Four Steps of Data Capture
Step 1: Chemical Makeup – When selecting or determining what plant material to use for extraction, processors first must examine the chemical makeup of the cannabis biomass. This can include the profiles of cannabinoids, terpenes, and the fat/wax/water content.
The exact chemical makeup of cannabis biomass can be difficult to determine because of its nonhomogeneous nature. Imagine closing your eyes and selecting a random sample from a container of bulk biomass. Maybe you grab a sugar leaf or flower, high in THC-laden trichomes, or maybe you grab a fanleaf with little to nothing to contribute to a high-quality extract. The chemical composition will look significantly different depending on how one selects the sample. So it’s important to be cognizant of what and how biomass testing is conducted, and often a single sample isn’t the answer. Knowing the approximate chemical makeup of the feedstock material will guide the processor to determine what type of recipe they will use for extraction and post processing and, ultimately, what end products are most valuable for a given input.
Once the chemical makeup has been determined, the processor will know the inputs of the material, such as the associated THC, CBD, terpenes, etc. They can then use that data to determine what will (or should) come out of the extraction process at its conclusion. This is the mass balance of the production process. It is difficult or impossible to optimize any process if one doesn’t know exactly what goes in and what comes out. Of course, this is much easier said than done given the nonhomogeneous nature of biomass.
Step 3: Identify and Maintain Key Process Parameters – Depending on the recipe and desired end product as determined through the above steps, the extraction process will need to maintain specific temperatures, pressures, times, and flow rates, among other key variables, to ensure a consistent, quality product. This is where a DoE or other similar process can add significant value. Analytical tools, such as the DoE, can help determine what process parameters need to be precisely controlled, and what parameters can have looser controls or can be ignored altogether. Compliance comes into play here as well. The ability to track and record these key data points is crucial to achieving GMP compliance as well as creating a consistent product that customers expect.
Step 4: Post Process Review – In order to understand how recipe parameters affect the end product, the processor needs to know its chemical composition as well as the composition of any waste materials (e.g., biomass, fats, waxes), or impurities that have been filtered out. Capturing this data is vital as it offers the critical clues to why a particular batch did not turn out as planned, for example, so the processor can investigate potential causes and corresponding solutions.
Step 5: Recording Data Between Each Process – What happens between each process is nearly as important as what happens during the process. Storage conditions can have an impact on quality and consistency, issues that may not be readily evident within the data capturing during processing. Those data points to know, among others, may include monitoring the freezer temperature where biomass is stored, measuring the humidity of the environment, documenting when and how equipment is cleaned, or even tracking how long material sits between extraction and placement in a vacuum oven.
Decision Making Via Data Analysis
After the data is captured and analyzed, managers may need to enact decisions if the data shows deviations from the expected outcomes. For example, as part of post-production lab tests (step 4), are acetone traces appearing in the finished product? If so, the organization may need to change its equipment cleaning practices (step 5) to ensure unwanted trace chemicals are not seeping into finished products.
Although enacting a program to better capture, review, and analyze data can appear to be a daunting task, doing so will provide the processor a significant competitive advantage. Not only will it help ensure consistent production while future-proofing the organization against coming regulations, it may also enable processors to experiment with and develop novel or proprietary extracts derived from a repeatable, scientific method that can’t easily be replicated by competitors.
Jack Naito is President of Luna Technologies, where he oversees operations, strategic growth, and R&D for the company he co-founded in 2016. Jack entered the cannabis industry after time spent as a Materials, Process, and Physics Engineer for aerospace giant Boeing. Jack obtained an Economics and Business degree from Colorado College and a Master’s degree in Mechanical Engineering from the University of Washington.
Luna Technologies engineers state-of-the-art extraction equipment for cannabis processors. The meticulously designed, automated equipment empowers operators to process fresh-frozen or cured plant biomass with stress-tested hardware and built-in failsafes to foster a superior level of workplace safety while also lowering labor costs. Luna’s Earth-conscious engineering approach helps decrease energy consumption while setting the industry standard for safety, quality, consistency, and customization in support of creating clean, consistent cannabis concentrates with medical and social benefits. Learn more at www.lunatechequipment.com.
Member Blog: Evaporation is Costing the Cannabis Industry Millions. Here’s Everything You Need to Know.
by Peak Supply Co
As cannabis ages, many of its therapeutic components degrade and transform into less effective compounds. Here’s everything you need to know about cannabis degradation, how the compounds are affected, and a few ways to restore products that have seen better days.
How long do cannabis and hemp buds stay fresh?
Cannabis is made up of various naturally occurring chemical compounds, including cannabinoids, terpenes, flavonoids, lipids, and fibers. Just like all organic materials, these components break down and degrade over time.
Think about your favorite fruits. Fresh oranges for example, will eventually rot as they age and their molecular compounds break down. When exposed to light, their outer layers start to spoil in a process known as photodegradation that causes discoloration and loss of flavor, vitamins, and proteins.
Further enzymatic chemical reactions occur and transform water, vitamins, and other molecules into different formations that can degrade even further with added heat or moisture loss. The oranges will lose their zesty aroma, sweet flavor and will be more susceptible to microbes, which will eventually cause the fruit to spoil. That said, dried fruits can be stored in a pantry for much longer before they’re no longer safe to eat as the “conditioning” or “curing” process can make them shelf-stable for up to a year.
Like dried fruits, cannabis and hemp undergo a curing process that helps to equalize the moisture content among the buds. This process reduces the risk of mold and spoilage while keeping the flower fresh, flavorful, and potent. Following this process correctly can keep cannabis and hemp flower “fresh” for 3-6 months or longer if stored properly. However, even with the most disciplined processes and practitioners, eventually, all organic materials begin to break down from exposure to the elements.
Much like our dried oranges example above, cannabis and hemp stored in suboptimal conditions are more susceptible to “rot” and can lose everything that makes them special. Light and temperature can contribute to the degradation of these natural features, but the biggest factor in terpene degradation is moisture content – or the lack of it. Moisture helps to preserve these compounds for prolonged periods of time.
What happens to the terpene profile and moisture content of cannabis and hemp over time?
On average, 12% of all cannabis and hemp biomass is moisture. As that moisture evaporates, it takes valuable terpenes and other essential oils with it leading to dry and brittle plant matter. Terpenes are naturally occurring chemical compounds found in plants that are responsible for their unique aromas and flavors. They also add and help preserve moisture. Cannabis and hemp contain an unparalleled profile of 100+ different terpene isolates that all evaporate at different rates based on temperature and humidity.
While live terpenes smell most potent during the flowering phase, terpene degradation starts immediately after the buds are cut from the stem. This happens because terpene oils, especially the most pleasant ones found in tiny amounts, tend to have low-temperature tolerance thresholds and evaporation levels. Once these terpenes have evaporated they will not be replaced by the living plant after cutting. This is why curing and storage is so important post-harvest. The curing stage allows for the terpene profile to mature but, even during this process terpene potency will continue to weaken.
When flower is stored below 50-55% RH (Relative Humidity) it leads to the fragile cannabinoid and terpene-rich trichomes to become brittle and break off. This lowers potency and causes the terpenes to evaporate with the remaining moisture content. The longer cannabis and hemp are stored in these conditions, the less potent, flavorful, and aromatic they become. On the other hand, going over 65% RH is in the danger zone of where mold can thrive and wreck a harvest with bona fide rot.
Who is affected by terpene and moisture degradation?
In short, terpene degradation affects everyone. Growers see the most significant profit loss as evaporation can take pounds and pounds of cannabis away from their final numbers in as little as 14 days. Dispensaries also see a loss of profit as the flowers dry during transit and while sitting on the shelf, making it so that they paid for more than what they actually ended up selling to their customers.
In the end, consumers are eventually the ones left holding the bag. Not only is the flower at its highest degradation stage by the time it gets into their hands but loss in weight can turn a pre-packaged 3.5g eighth into 3.15 grams or less.
The example in the graphic below outlines how moisture degradation affects both yields and profit.
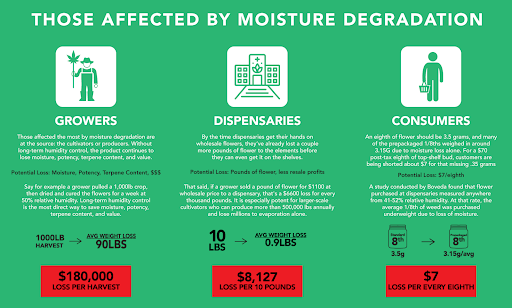
How can you stop your cannabis from drying out?
Using orange peels and pieces of bread for rehydration used to be the norm in what feels like ages ago. In the more recent past, cultivators, dispensaries, and consumers alike have relied heavily on moisture-control products like Boveda brand or Boost brand humidity packs. These products can help to keep moisture in the 50-65% optimal range. However, they do have their drawbacks.
The humidity packs have a definite shelf life and in extremely dry conditions, they can’t keep up with the rate of evaporation – almost to the point where many claim they don’t actually work. While they can help maintain some moisture content, they can’t rehydrate buds that have gone below the 50% humidity threshold. This makes them closer to a moisture stabilizer of sorts than a moisture booster or replenisher. Beyond using the aforementioned “ancient ways” to rehydrate abused cannabis flower, these packs have been the only option available to the industry.
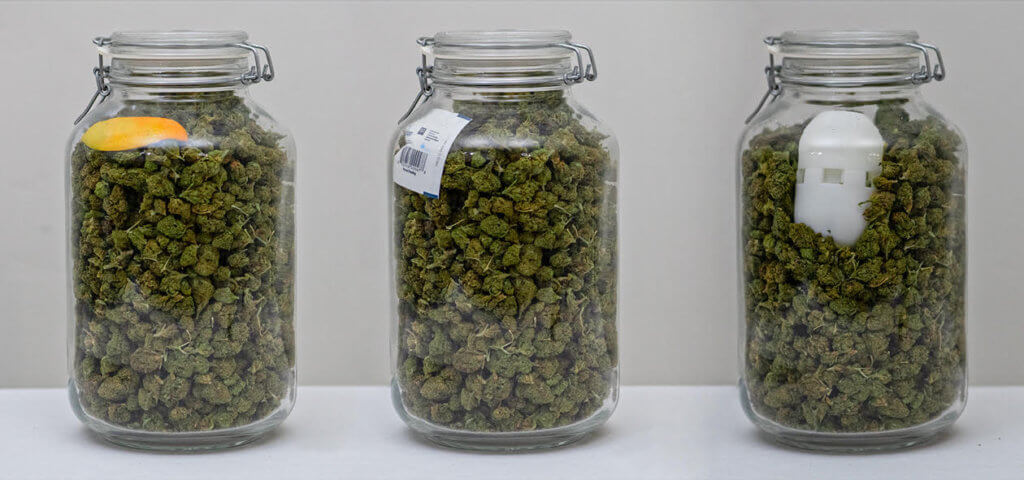
However, recently a new product on the market called the “Cure-Egg” has been making waves and has been proving invaluable when it comes to product reclamation and preservation. The Cure-Egg’s patented ergonomic design and utility works in a similar way to the hydration packs but boasts the ability to rapidly rehydrate biomass in a few days’ time while staying under the mold growth threshold.
In addition to its ability to quickly rehydrate cannabis and hemp flower it also comes with the added benefit of terpene infusion to counteract terpene loss. Oftentimes beautiful-looking flower is grown but it somehow misses the mark when it comes to the nose. This product could be a game-changer for farms, dispensaries or anyone sitting on older product that has lost its zing from prolonged storage or errors in production.
Users are quickly finding out that they can take less than premium flower destined for the world of “affordable pre-rolls” and easily turn them into a flavor and aroma-packed desirable product that doesn’t have to come at a discounted price. Time will tell if this product will become the next industry staple but one thing is for certain, innovative new products are definitely shaking things up.
Peak Supply Co provides the first true all in one solution providing terpenes, vape cartridges, package design and production, helping clients progress from starting creative to finished product.